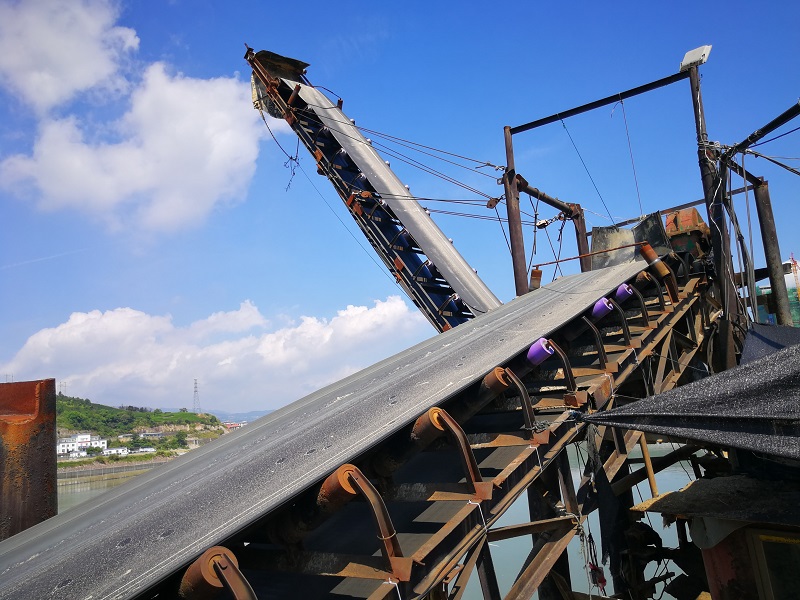
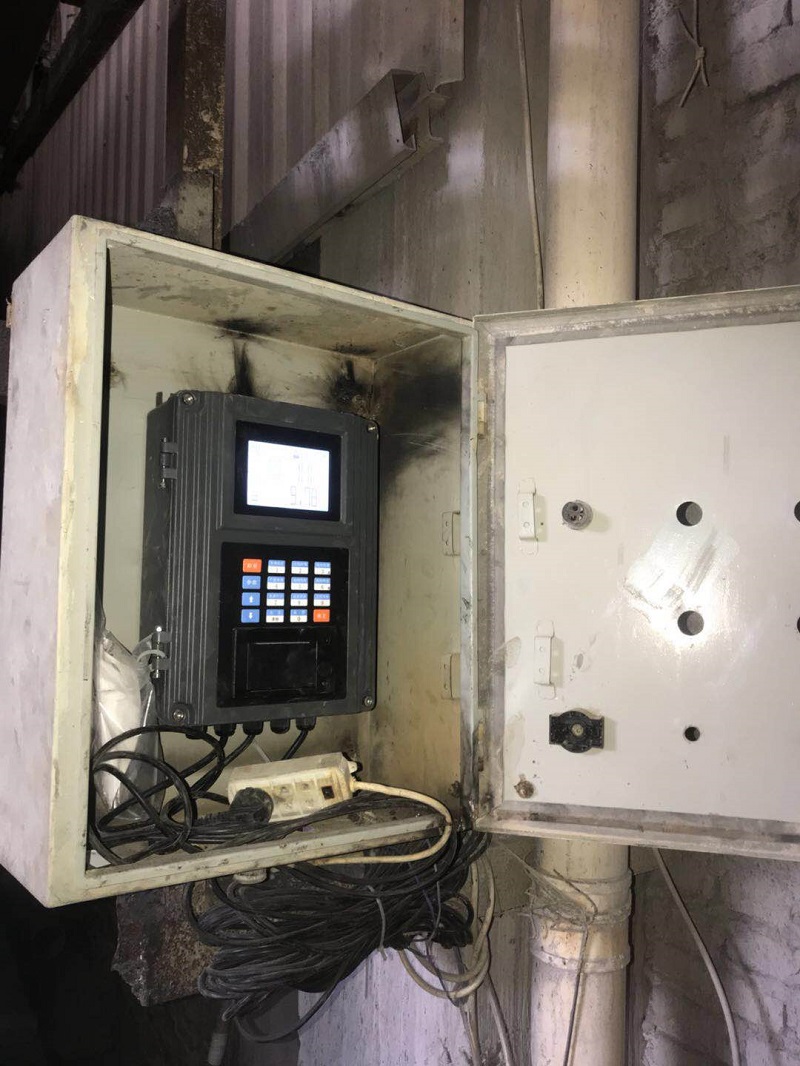
1. ကောင်းမွန်စွာ ချိန်ညှိထားသော အီလက်ထရွန်းနစ် ခါးပတ်စကေးကို ကျေနပ်လောက်ဖွယ် ပုံမှန်လည်ပတ်နိုင်စေရန်၊ ကောင်းမွန်သော တိကျမှုနှင့် ယုံကြည်စိတ်ချရမှုကို ထိန်းသိမ်းရန် စနစ်ပြုပြင်ထိန်းသိမ်းမှုဆိုင်ရာ အလုပ်များကို လုပ်ဆောင်ရန် အရေးကြီးပါသည်။ အောက်ပါ ကဏ္ဍခုနစ်ရပ်ကို အသုံးပြု၍ ထိန်းသိမ်းသင့်သည်- ပထမ၊ တပ်ဆင်မှုအသစ်အတွက်၊ တပ်ဆင်ပြီးနောက် လအနည်းငယ်အတွင်း အီလက်ထရွန်းနစ်ခါးပတ်စကေး၊ တိကျမှုလိုအပ်ချက်များနှင့် ရုပ်ပိုင်းဆိုင်ရာချိန်ညှိခြင်း သို့မဟုတ် စီစဥ်ချိန်ညှိခြင်း၏ အချိန်မီရွေးချယ်မှုအရ၊ ကြားကာလတန်ဖိုးကိုသိရှိရန် ရက်သတ္တပတ်ခြားတစ်ကြိမ်၊ သုညကိုသိရှိရန် အခြားရက်သတ္တပတ်တိုင်း၊ဒုတိယအချက်၊ အလုပ်ပြီးချိန်တိုင်းတွင် ကော်စကေးပေါ်ရှိ ကော်စကေးများ အစုလိုက်နှင့် ကော်တိပ်များကို ဖယ်ရှားရန် အချိန်မီပိတ်ပါ။တတိယအချက်၊ တိပ်၏လည်ပတ်မှုအတွင်း၊ တိပ်သည် သွေဖည်သွားခြင်းရှိမရှိ မကြာခဏ စစ်ဆေးသင့်သည်။စတုတ္ထ၊ အလေးချိန် roller လှုပ်ရှားမှု၏ပြောင်းလွယ်ပြင်လွယ်ကြောင့် radial runout degree သည် တိုင်းတာမှုတိကျမှု၊ လေးလံသော roller ချောဆီ၏ symmetry ကိုတိုက်ရိုက်အကျိုးသက်ရောက်မည်ဖြစ်ပြီး တစ်နှစ်လျှင် 1 ~ 2 ကြိမ် အလေးချိန်ရှိသော roller ချောဆီအား အာရုံစိုက်ကာ အီလက်ထရွန်းနစ်ကို ပြန်လည်ချိန်ညှိရန်လိုအပ်ပါသည်။ ခါးပတ်စကေး;ပဉ္စမ၊ အသုံးပြုမှုလုပ်ငန်းစဉ်တွင်၊ ပုံမှန်စီးဆင်းမှုကို ချိန်ညှိထားသော စီးဆင်းမှုပမာဏ၏ ±20% အကွာအဝေးအတွင်း အကောင်းဆုံးထိန်းချုပ်ထားသည်။ဆဌမ၊ အမြင့်ဆုံးစီးဆင်းမှုသည် 120% ထက်မပိုဘဲ၊ ၎င်းသည် အီလက်ထရွန်းနစ်ခါးပတ်စကေး၏ တိကျမှုကို တိုးတက်စေရုံသာမက စက်ကိရိယာများ၏ ဝန်ဆောင်မှုသက်တမ်းကိုလည်း မြှင့်တင်ပေးမည်ဖြစ်သည်။သတ္တမအချက်၊ အာရုံခံကိရိယာတပ်ဆင်မှု၏စကေးကိုယ်ထည်တွင် ဂဟေဆော်ခြင်းအား တားမြစ်ထားသည်။ အထူးကိစ္စများတွင် ပါဝါထောက်ပံ့မှုကို ဦးစွာဖြုတ်ပြီးနောက် မြေစိုက်ကြိုးကို စကေးကိုယ်ထည်သို့ ပို့ဆောင်၍ မထားသင့်ပါ။ အာရုံခံကိရိယာမှတဆင့်လက်ရှိလှည့်ပတ်။
2.System overhaul and maintenance သည် ပြင်ပအချက်များကြောင့်၊ အီလက်ထရွန်းနစ်ခါးပတ်စကေး၏ ချို့ယွင်းမှုကို စစ်ဆေးပြီး ဖယ်ရှားပစ်ရန်၊ အခြားသော အလေးချိန်ယန္တရားနှင့် နှိုင်းယှဉ်ပါက ပိုမိုရှုပ်ထွေးသည်၊ ပြုပြင်ထိန်းသိမ်းရန် လိုအပ်သော ဝန်ထမ်းများသည် သက်ဆိုင်ရာ အီလက်ထရွန်းနစ် ခါးပတ်စကေးစကေး အသိပညာနှင့် ညွှန်ကြားချက်လက်စွဲကို ဂရုတစိုက်ဖတ်သင့်သည်၊ မကြာခဏ အကဲခတ်ခြင်း၊ မကြာခဏ စတင်ခြင်း၊ ခွဲခြမ်းစိတ်ဖြာတွေးခေါ်ခြင်းနှင့် အနှစ်ချုပ်ခြင်းတို့ဖြင့် ပိုမိုလုပ်ဆောင်ပါ။
(၁) Computer integrator maintenance computer integrator သည် electronic belt scale ၏ အဓိက အစိတ်အပိုင်းဖြစ်ပြီး mV signal ကို အလေးချိန် sensor မှ digital signal သို့ ပေးပို့ပြီးနောက် ပုံဖော်ခြင်းအတွက် pulse signal မှ ပေးပို့သော speed sensor ကို ပေါင်းစပ်ကာ အတွင်းသို့ ပေးပို့ပြီး၊ microprocessor သည် centralized processing ဖြစ်သောကြောင့် ပုံမှန်ထိန်းသိမ်းရန် လိုအပ်ပါသည်။
(၂) အလေးချိန်အာရုံခံကိရိယာနှင့် အမြန်နှုန်းအာရုံခံကိရိယာ အလေးချိန်အာရုံခံကိရိယာနှင့် အမြန်နှုန်းအာရုံခံကိရိယာသည် အီလက်ထရွန်းနစ် ခါးပတ်စကေး၏ နှလုံးသားဖြစ်သည်။အမြန်နှုန်းအာရုံခံကိရိယာအား တိပ်နှင့်ထိတွေ့သော လှိမ့်စက်တစ်ခုမှ မောင်းနှင်ပြီး တိပ်၏အမြန်နှုန်းအချက်ပြမှုကို ဗို့အားအချက်ပြမှု (စတုရန်းလှိုင်း) အဖြစ်သို့ ပြောင်းလဲသွားသည်။ထုတ်လုပ်သူမှ ရွေးချယ်ထားသော မတူညီသော စက်ပစ္စည်းများနှင့် တိပ်၏ မတူညီသော လည်ပတ်နှုန်းကြောင့် ဗို့အားပမာဏမှာလည်း ကွဲပြားပါသည်။ပုံမှန်အလုပ်အခြေအနေအောက်တွင်၊ ဗို့အားပမာဏသည် ယေဘုယျအားဖြင့် 3VAC ~ 15VAC ကြားဖြစ်သည်။စစ်ဆေးရန်အတွက် multimeter ၏ "~" ဖိုင်ကို အသုံးပြုနိုင်သည်။
(၃) Zero point correction သုညအမှတ် ထပ်ခါတလဲလဲ ချိန်ညှိခြင်းသည် မမှန်ကန်သောအလေးချိန်ကို ဖြစ်ပေါ်စေရန် ခွင့်မပြုပါ။ပထမဦးစွာ၊ အခင်းဖြစ်ပွားရာနေရာမှစတင်သင့်သည်၊ အကြောင်းရင်းသည် အတိုင်းအတာကိုယ်ထည်တပ်ဆင်မှုနှင့် ပတ်ဝန်းကျင်အသုံးပြုမှု အရည်အသွေးနှင့် ဆက်စပ်နေနိုင်ပြီး၊ အောက်ပါအချက်များမှ ကိုင်တွယ်ဖြေရှင်းနိုင်သည့် တိကျသော၊
① ပတ်ဝန်းကျင် အပူချိန်နှင့် စိုထိုင်းဆသည် နေ့ရောညပါ ပြောင်းလဲခြင်းရှိမရှိ၊ ၎င်းသည် conveyor ခါးပတ်၏ တင်းမာမှု အပြောင်းအလဲများကို ဖြစ်ပေါ်စေနိုင်သောကြောင့် အီလက်ထရွန်းနစ် ခါးပတ်သည် ဟန်ချက်မညီဘဲ သုညပျံ့သွားစေရန်၊(၂) စကေးပေါ်တွင် ဖုန်မှုန့်များ စုပုံနေခြင်း ရှိ၊ မရှိ၊ သယ်ယူပေးသည့် ခါးပတ်သည် စေးကပ်နေပါက အချိန်မီ ဖယ်ရှားသင့်သည်။ပစ္စည်းသည် စကေးဘောင်တွင် ပိတ်မိနေသလား၊④ Conveyor belt ကိုယ်တိုင်က ယူနီဖောင်းမဟုတ်၊⑤ စနစ်သည် ကောင်းမွန်စွာအခြေခံထားခြင်းမရှိပါ။⑥ အီလက်ထရွန်းနစ် တိုင်းတာရေး အစိတ်အပိုင်း ချို့ယွင်းမှု၊⑦ အလေးချိန်အာရုံခံကိရိယာသည် ပြင်းထန်စွာ ဝန်ပိုနေပါသည်။ဒုတိယအနေဖြင့်၊ အာရုံခံကိရိယာ၏တည်ငြိမ်မှုနှင့်ကွန်ပြူတာပေါင်းစည်းခြင်း၏စွမ်းဆောင်ရည်ကိုထည့်သွင်းစဉ်းစားသင့်သည်။
တင်ချိန်- စက်တင်ဘာ ၁၄-၂၀၂၂